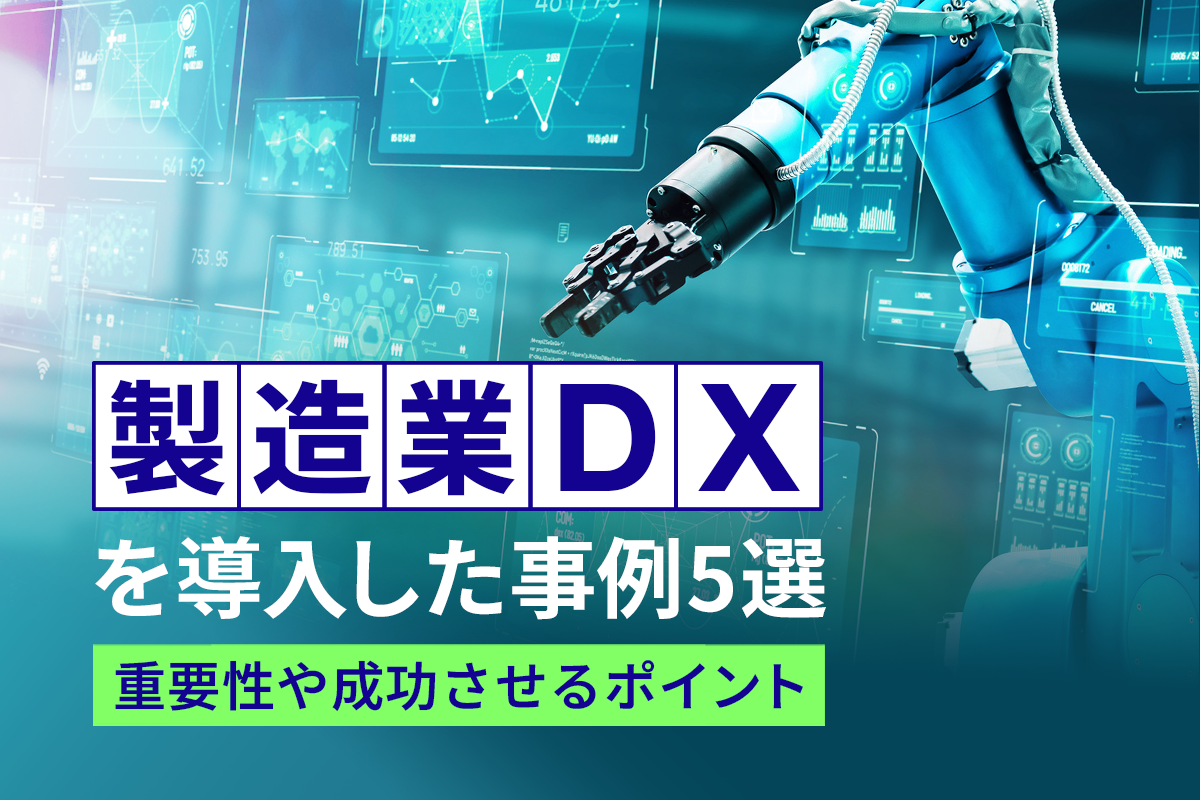
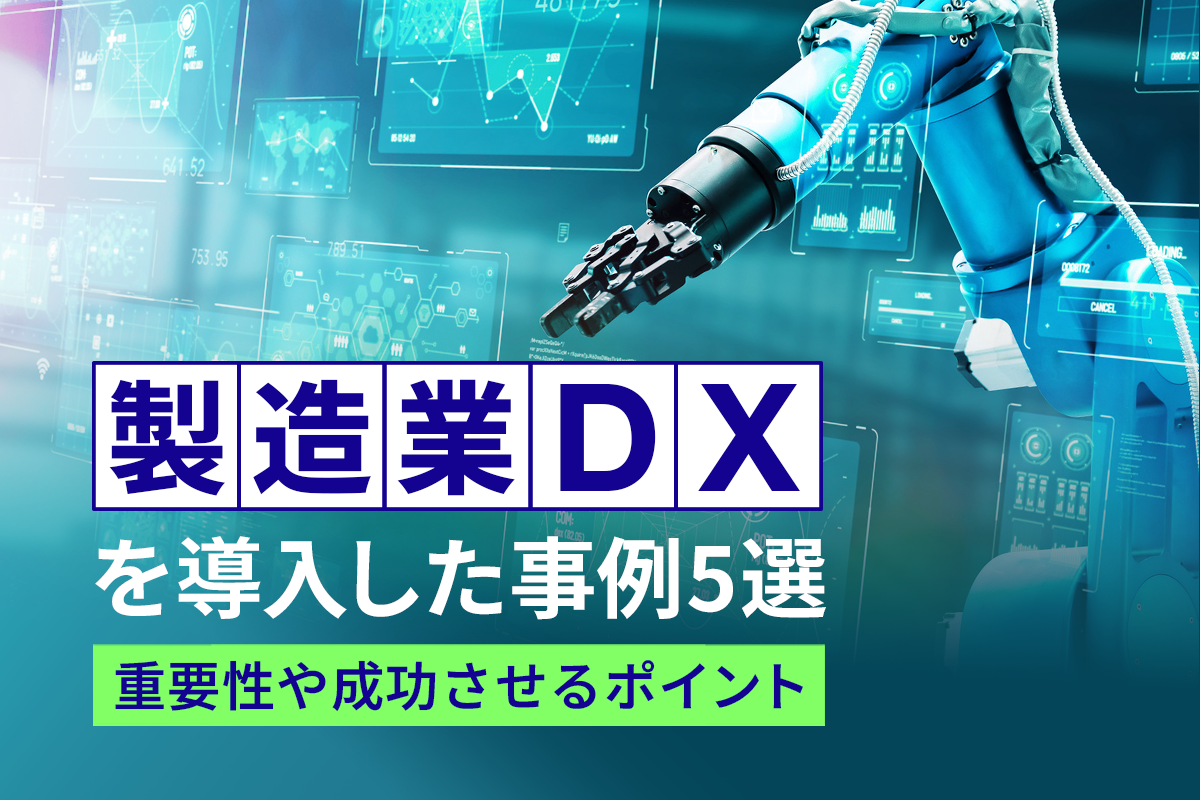
製造業の企業にとって、生産効率の向上は競争力を上げるために重要なテーマです。しかし、生産効率と一口に言ってもさまざまな計算方法があります。
そこで本記事では、製造業における重要な指標である生産効率の意味や計算方法のほか、生産効率向上を達成するポイントを紹介します。労働の担い手が減少している昨今、人手不足に陥り、生産効率をなかなか追求できないとお悩みの方はぜひ参考にしてみてください。
この記事でわかること
|
製造業ではさまざまな指標を使って業績を評価しますが、生産効率もその一つです。ここでは生産効率の意味と計算方法について解説します。
生産効率とは、どの程度のコストでどれだけの生産ができたかを測る指標のことです。具体的には、生産に必要な人件費や時間などのコストに対して、実際にはどのくらいのコストで生産できたかを表したものです。投入しているコストの無駄が少ないほど、生産効率が良いことになります。
企業には「利益率を◯%上げる」「コストを◯%低減する」「顧客満足度を上げる」など、さまざまな業績目標があります。これらの目標を達成するためには、不良率や稼働率といったKPI(重要業績評価指標)を活用し、各現場の進捗状況を定量的に評価することが大切です。生産効率もKPIの一部として重要な役割を担っています。
生産効率には3種類の計算方法があります。生産効率は、生産しているものや生産方式などによって計算式が変わることに注意が必要です。
基本的には、以下の計算式のように、生産量から考えるケースが多いでしょう。
生産効率 = 実際の生産量 ÷ 理論上の最大生産量 × 100 |
実際の生産量とは、言葉のとおり、実際に生産できた製品の量や数量です。一方の理論上の最大生産量とは、設備や作業時間をフルに活用した場合に達成可能な生産量の最大値を指します。
機械の生産効率を考える場合は、機械の稼働時間を軸に算出する方法もあります。
生産効率(可動率)= 実際の稼働時間 ÷ 本来稼働すべき時間 × 100 |
この方法は、機械が実際にどの程度正常に動いていたかで生産効率を判断するもので、いわゆる「可動率(べきどうりつ)」と意味は一緒です。たとえば、本来稼働すべき時間が8時間だった場合、実際に機械が動いていた時間も同じ8時間ということはほぼありません。
その理由は、製造中には品種の切り替えを行う段取り替えや、前工程の遅れによる部品待ち、設備トラブルによるチョコ停など、さまざまな要因によって機械が停止する時間が少なからずあるためです。
生産を効率よく進めるには、機械の停止時間をいかに短くするかが重要です。本来稼働すべき稼働時間が8時間の機械について、実際には4時間稼働した場合と、現場の改善によって稼働時間が5時間に伸びた場合とで比較すると、生産効率は12.5%も違います。
ほかにも、1人あたりの出来高数を軸に生産効率を考えるケースもあります。
生産効率(1人あたりの出来高数) = 出来高数 ÷ 人数 |
以上の3種類の計算方法は、自社の生産方式や形態に合わせて選択しましょう。射出成形機やプレス機を活用する現場であれば可動率を採用でき、組み立て製造業などでは生産量から効率性を評価できるでしょう。
単純に考えれば、生産効率を上げるには生産性を上げればよいように思えます。しかし、本当にそうでしょうか。
生産性とは、製造した量を投入したコストで割ったもので、少ない人数・工数でたくさん生産すれば、その分生産性は高まります。
実は、生産性がアップすることで生産効率が低下するケースがあります。たとえば、生産性が向上したことで仕掛品や売掛品の在庫が増加した場合、在庫の保管や出入庫作業などのコストが増すことになります。このように、管理コストの増加によって全体としての生産効率が低下する可能性があるのです。
生産効率や生産性といった指標は、状況や目標によって以下のように使い分ける必要があります。
生産性と生産効率は、総合的に判断し、状況に併せてそれぞれ改善することが重要です。
生産効率をアップさせる方法にはどのようなものがあるでしょうか。ここでは、生産効率をアップさせるためのポイントについて紹介します。
生産効率をアップさせるには、まず生産現場の現状を知ることが大切です。「生産量はボトルネック工程で決まる」とよく言われています。たとえば、工程別の一日の生産能力がA工程400個、B工程250個、C工程300個だったとしましょう。
この場合、A工程やC工程の生産効率をどれだけ上げても、一日の最終的な生産量はB工程の250個で決まってしまいます。したがって、まずはボトルネック工程であるB工程の生産効率を上げることに注力しなければなりません。すべての工程や生産ラインを可視化し、どこがボトルネックかを探ることから始めましょう。
ボトルネック工程が見つかったら、なぜその工程の生産効率が悪いのか、原因を探ります。原因は5Sや3Mに該当することが多いため、まずはそこから探ることがおすすめです。5Sとは「整理・整頓・清掃・清潔・しつけ」のことです。たとえば、生産に必要な工具や材料を探すのに手間取っている場合、整頓や整理を徹底すれば効率よく仕事にあたれます。
3Mは「ムリ・ムダ・ムラ」のことです。生産現場では、どこかに過剰な負荷がかかっていたり、従業員ごとに作業量のバラつきがあったりするものです。このような3Mは生産効率を下げる要因であるため、優先的に改善することが大切です。
効率化についてさらに詳しく知りたい方は、以下の記事もご覧ください。
生産の効率化には、生産計画や人員計画を含めた生産管理の見直しが欠かせません。特に人員計画がうまくいかず人手不足に陥ると、製造現場にムリがかかり、作業ミスや長時間労働につながるといった悪影響があります。
そこで、各作業者がさまざまな工程に対応できるようにする多能工化や、業務を標準化し、特定の人にしかできない属人化の解消を進めることが業務効率につながります。もちろん、営業や生産管理、製造現場が連携し、早期に人員のリソースを把握することも大切です。あらかじめ人材が不足していることがわかれば、採用の強化などの対策を選択可能なためです。
生産効率には3つの計算方法があり、自社の生産方式などに合わせて算出すれば、評価指標として有効活用できます。
生産効率をアップさせるには、まず現在の生産現場の状況を定量的に把握することが重要です。次に、ボトルネック工程や作業効率を阻害する原因を特定し、それぞれに対策を施していきます。現場の改善だけでなく、人員計画といった生産体制の見直しも、生産効率には欠かせない要素です。
とはいえ、社内の業務改善を行いたいものの、そもそもリソースが不足しているという企業は多いでしょう。このような場合は、人材派遣を活用して必要な人員を確保するのがおすすめです。日研トータルソーシングなら、若手から現状の業務を引き継ぐ即戦力人材まで、ニーズに合った人材を紹介できます。人手不足を解消し業務効率を達成したい担当者の方は、以下の資料をご覧ください。