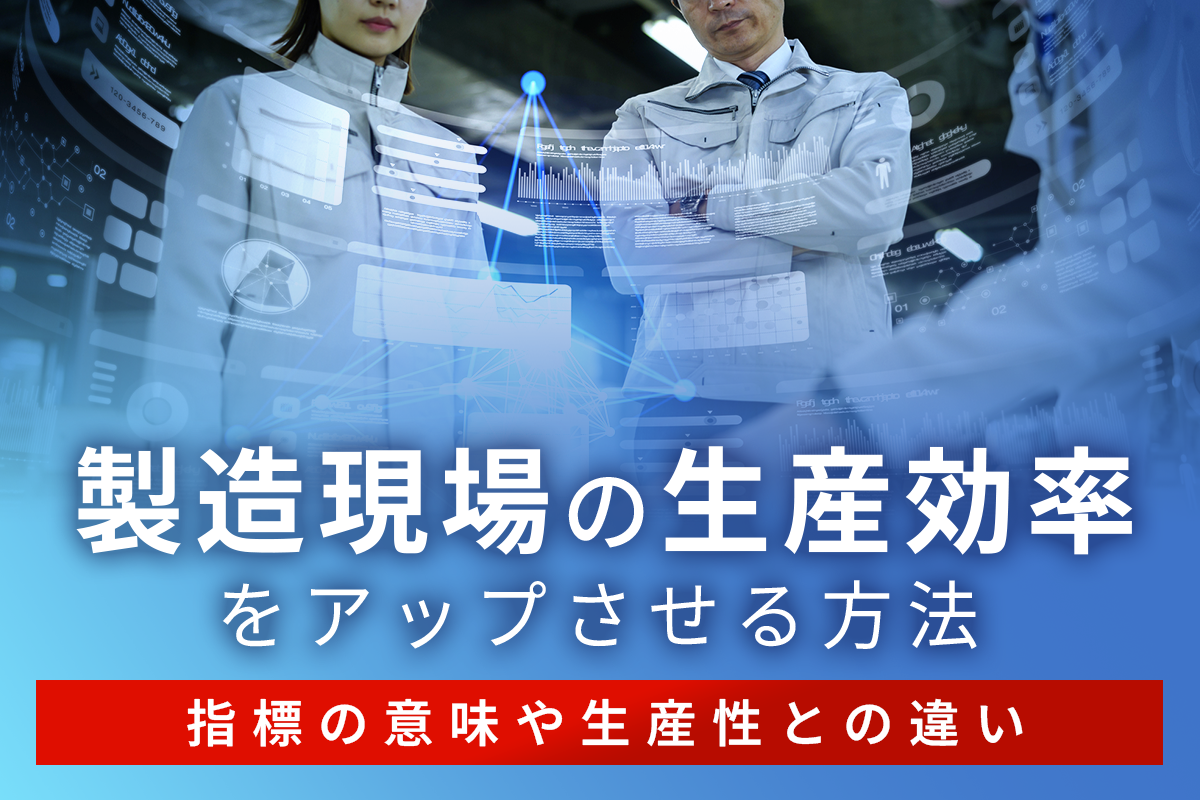
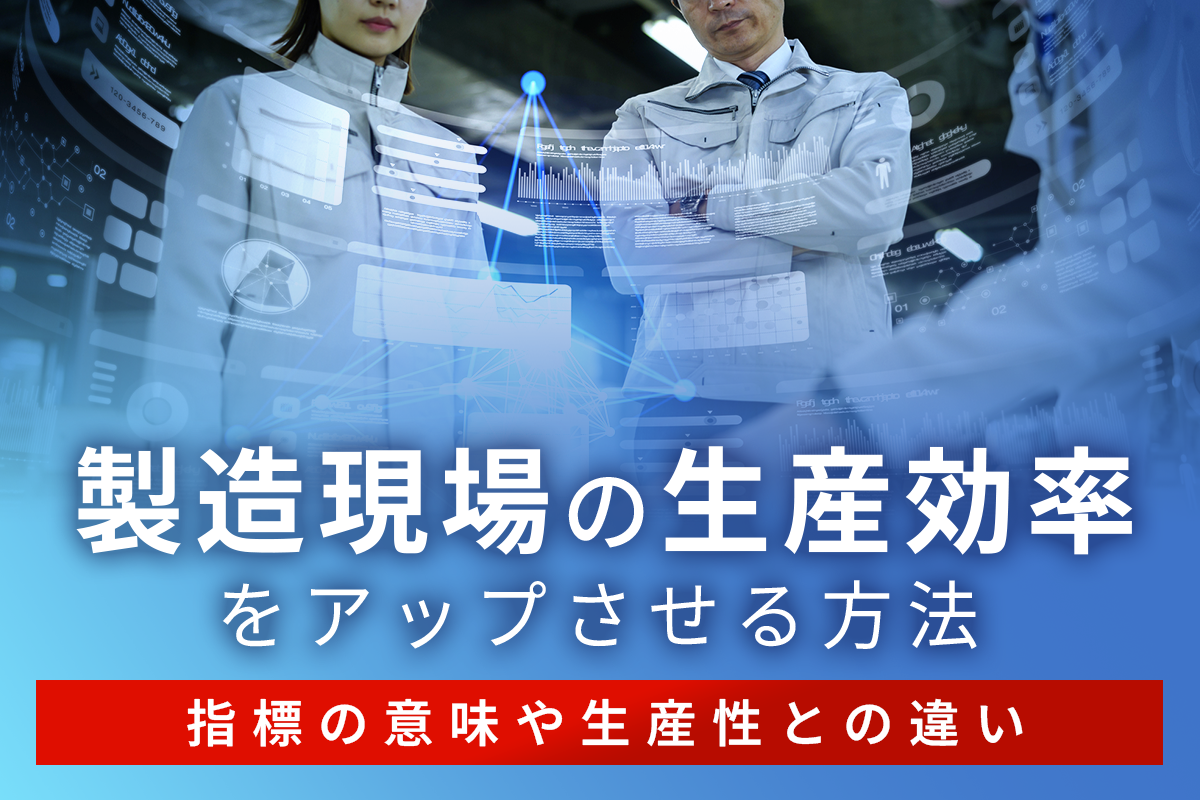
昨今はさまざまな業界においてDXが進められていますが、製造業も例外ではありません。企業の価値や競争力を高めるために欠かせないDXをどのように推進するかが、ビジネス拡大や企業成長のカギと言えるでしょう。
本記事では、製造業のDXの成功事例を詳しく解説します。DXをどのように取り入れるかを検討している製造業の企業担当者は、ぜひ参考にしてください。
この記事でわかること
|
製造業のDX成功事例を5つご紹介しましょう。
課題 |
・「マスカスタマイゼーション」への対応 ・工場ごとに図面の描き方や技術標準が異なる |
実施したこと |
・設計部門が作成する図面などの各種設計情報をオンライン上で共通化 |
効果 |
・人材配置の柔軟性が向上 ・工場間の業務負荷を分散させ、人手不足に対応することにも成功 |
電機メーカーの沖電気工業株式会社(以下、沖電気)は、大量生産と個別受注生産を組み合わせる生産方式である「マスカスタマイゼーション」への対応や、社会の変化による需要減少に大きな危機感を抱いていました。
さらに、工場ごとに図面の描き方や技術標準が異なっていることや、共通する部品であっても、共通の仕様では生産できないといった課題にも直面していたそうです。
そこで、沖電気は「バーチャル・ワンファクトリー」を導入し、設計部門が作成する図面などの各種設計情報を共通化しました。
バーチャル・ワンファクトリーとは、複数の工場をデジタル技術で連携させ、あたかも一つの工場のように機能させる仕組みです。この導入により、設計部門から出される図面などの各種設計情報を共通化させました。
具体的には、工場ごとの生産形態の特徴や製造に対する考え方、知見をまとめて整理・把握し、設計データをオンライン上で受け取れるように工夫して、バーチャルで工場間の横串連携を推進したのです。
その結果、工場間の人材や技術交流が活発となり、図面の描き方や技術標準が統一されたことで、人材配置の柔軟性が向上しました。さらに、工場間の業務負荷を分散させ、人手不足に対応することにも成功したのです。
課題 |
・製品の多様化 ・カスタマイズ性能の向上 ・納期の短縮化 ・技術継承の強化 |
実施したこと |
・開発プロセスのコンカレント化 |
効果 |
・製品開発プロセスの手戻り減少による納期短縮に成功 |
大手電機メーカーの富士通株式会社(以下、富士通)では、製品開発についてさまざまな課題が存在していました。たとえば、市場のニーズや環境の変化による製品の多様化やカスタマイズ性能の向上、納期の短縮化、技術継承の強化など、製品開発部全体の連携強化が求められていたのです。
そこで富士通は、DX推進の取り組みとして「富士通生産方式(FJPS)」を確立し、開発プロセスのコンカレント化を目指しました。設計・開発のデジタルプラットフォームである「FTCP」の構築や、試作品を作らずに3Dシミュレーターで行うデザイン・不具合の検証により、 製品開発プロセスの手戻り減少や品質向上、納期短縮を達成したのです。
情報の一元化によって製品開発におけるノウハウや知識を収集し、必要な部署間で情報の共有ができました。
課題 |
・顧客からのデータや製造チームから得たデータをタイムリーにフィードバックしにくい |
実施したこと |
・工場横断型のプラットフォームの構築 |
効果 |
・プラットフォームを活用したプロジェクトの立ち上げや取り組みの数が増え、費用対効果向上に成功 |
日本が誇るグローバル企業であるトヨタ自動車株式会社(以下、トヨタ)は、これまで3D CADデータや試作時の特性データのようなさまざまなデジタルデータを活用して、技術開発や生産準備に一定の成果を上げてきました。一方で、顧客からのデータや製造チームから得たデータをタイムリーにフィードバックすることに苦戦をしていたそうです。
そこで、工場横断型のプラットフォームの構築に力を入れることにしました。社内部署による組織的な教育支援を行い、BI(ビジネス・インテリジェンス)やAIなどの便利ツールをプラットフォーム上に用意することで、従業員がDX導入に苦戦しないように工夫を施したのです。
その結果、それぞれの事業部や工場において、プラットフォームを活用したプロジェクトの立ち上げや取り組みの数が増え、費用対効果向上に成功しました。
また、工場IoTで得られた成果を受け、エンジニアリングチェーンやサプライチェーンのデジタル化に向けても動き始めています。
課題 |
・特定の製造担当者の知見や技術力に依存している ・生産現場の機械化・省人化を行いたい |
実施したこと
|
・回路図面と配線図面のデータを融合して配線図データを作成するシステムの導入 |
効果 |
・IWSを用いて事前に設計・データ化することで、フロントリーディングの実現に成功 |
自動化制御盤メーカーである株式会社アイデン(以下、アイデン)は、特定の製造担当者の知見や技術力に依存している「属人化」の状況を打破するため、そして長年課題となっていた生産現場の機械化・省人化に向けて、「IWS」を導入しました。
IWSとは「I-DEN Wiring Solution」の略称であり、回路図面と配線図面のデータを融合して配線図データを作成するシステムです。このシステムの導入により、機械化できる部分は機械に頼り、熟練技術者はより付加価値の高い業務に専従するという形をとれるようになりました。製造担当者による工程設計部分において、IWSを用いて事前に設計・データ化することで、フロントリーディングの実現に成功したのです。
さらに、作業量が明確になったことで、材料の必要量を事前に把握でき、製造担当者の進捗管理もしやすくなりました。
課題 |
・製造コスト削減 ・製品差別化による競争力強化 |
実施したこと
|
・「製造現場データの発掘」「データの収集と統合」「データの見える化と分析」「顧客への価値提供」の4つを実現できるプラットフォームを整備 |
効果 |
・生産状態の可視化や生産計画の最適化を図ることで、ロス削減に成功 |
家電の製造・販売を行うダイキン株式会社(以下、ダイキン)は、多品種混合生産や需要変動に柔軟に対応できるような生産体制を構築してきました。しかし、市場変化のスピードが上がってきたことから、「マスカスタマイゼーション」を念頭に置いたものづくりを行い、製造コスト削減と製品差別化による競争力強化を図る必要に迫られました。
そこで、ダイキンは、大阪の堺市に新工場(デジタル・ファクトリー)を設立し、「製造現場データの発掘」「データの収集と統合」「データの見える化と分析」「顧客への価値提供」の4つから成るサイクルを構想しました。このうちの「データの収集と統合」の実現に向けて、工場のすべての設備をネットワークでつなぐ「工場IoTプラットフォーム」も整備したのです。
工場IoTプラットフォームにより、生産状態の可視化や生産計画の最適化を図ることで、ロス削減に成功しました。さらに、設備の故障や異常、生産の遅れを事前に検知する体制を整備し、生産体制の柔軟化も実現しました。
近年の製造業界ではさまざまな理由からDXの重要性が高まっています。
慢性的な人手不足への対策はもちろん、開発力強化のために開発手法や情報共有などの分野におけるDXを推進する企業も少なくありません。製造業におけるDX推進は、少子高齢化やグローバル化など、製造業を取り巻く課題を解決する手段といっても過言ではないでしょう。
製造業においてDXを推進するためには、従来のやり方から大きく方向転換する必要があり、現場に定着するまでに一定の時間がかかります。そのため、経営層から現場の従業員まで、DX推進の意義に対する共通認識を持たなければなりません。
それと同時に、適切な人材確保や人材育成にも力を入れる必要があります。DX推進に必要な人材を確保しなければ、そもそも成功は難しいと言えるでしょう。
製造業DXは、製造業出身者や製造業に対する支援経験がある人材によるサポートが必要不可欠です。現場で活躍するIT人材だけでなく、DX案件の経験を持つマネージャークラスの人材も登用しましょう。
社内で人材を育成する方法もありますが、どうしても時間がかかるものです。製造業DXを迅速に推進するためには、外部人材の支援も検討してください。
本記事では、製造業DXの代表的な成功事例を紹介しました。製造業だけでなく、さまざまな業界においてDXの重要性が叫ばれていますが、なかなか導入できずにお困りの企業様は多く存在します。
自社でDX推進に向けた適切な人材の確保が難しい場合は、外部の人材登用も併せて検討する必要も出てくるでしょう。もし、製造業におけるDX推進のための即戦力人材をお探しの場合は、ぜひ「日研トータルソーシング」にお任せください。
豊富な知識を持つ日研トータルソーシングでは、スタッフへの研修教育力とサポート力を強みに、質の高い人材サービスを提供しています。製造業の業務効率化や生産性向上に向けた具体的な相談はもちろんのこと、製造現場のさまざまな課題や問題点についても随時相談を承ります。ぜひ、お気軽にお問い合せください。