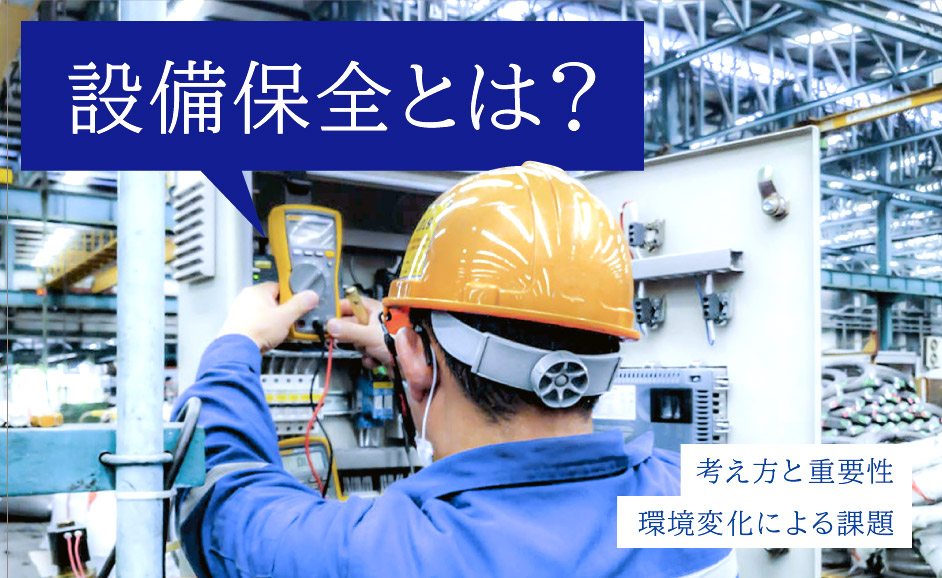
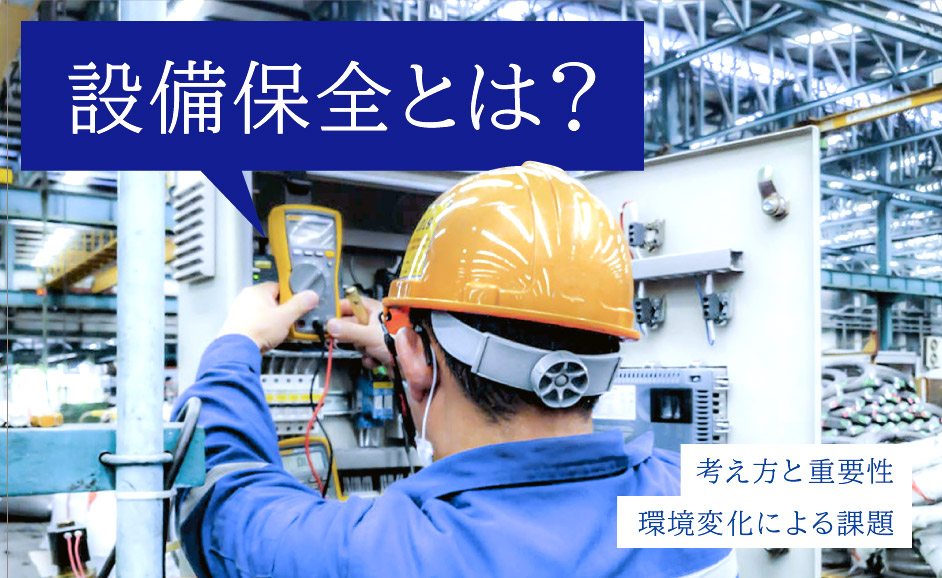
製造業の現場では「5S」の張り紙がよく見かけられます。作業の効率化や生産性の向上につながる大きなメリットがある反面、5S活動をスタートしたものの形骸化してしまい、かえってデメリットが懸念されてしまうケースも少なくありません。
5Sの導入にあたっては、推進するための体制づくりと従業員の理解が不可欠です。5Sとは何か、目的や効果などを解説したうえで、進め方のポイントを紹介していきます。
お役立ち資料はこちら
5S(読み方:ごエス・ごーエス・ファイブエス)とは製造現場での職場環境改善のための活動で、「整理」「整頓」「清潔」「清掃」「しつけ」の5つの言葉のローマ字の頭文字をとったものです。なお、「整理」「整頓」「清潔」の3つから3Sと呼ばれることもあります。
「整理」は不要なものを処分すること、「整頓」は必要なものを使いやすい場所に置くこと、「清掃」はきれいに掃除して点検を行うこと、「清潔」は清潔な状態を維持すること、そして「しつけ」は4つの「S」を習慣づけることを指すものです。
「整理」とは、必要なものと不要なものに分けて不要なものを処分することです。
大量の製品を製造する現場では、日々、多かれ少なかれ廃棄するべきものが出ます。不要なものをそのままにしていると、事故につながるリスクを招き、必要なものを探すときには手間がかかります。そのため、不要なものは溜め込まずに処分するべきなのです。
たとえば、在庫品に年ごとに色の違うシールを貼り、年数が経過して使えないものは順次処分するといった取り組みを行います。
「整頓」は、使う人が使いやすいように、資材や工具といった製造に必要なものを作業手順や使用頻度を考慮して、決められた場所に置くことです。
たとえば、工具の定位置を決めた場合、持ちだした際には「使用中」のプレートを置くといった運用を行います。資材や工具が定位置に置いてあれば、ものを探す手間が軽減され、スムーズに作業を進めることができるのです。
「清掃」は、作業場や製造機械などの清掃や点検といったメンテナンスを行い、きれいでいつでも使える状態に保つことです。
適切に清掃を行うことは、不具合や異常を発見しやすい体制構築につながります。具体的には、場所ごとに当番制で清掃の担当者を決めるといった方法が考えられるでしょう。
「清潔」はマニュアル化などによって整理・整頓・清掃を継続的に行い、清潔な状態を維持することです。より良い職場環境を維持することを促す効果もあります。
「しつけ」は4つの「S」を習慣づけるなど、職場の規律やルールを守ることを身につけることです。5S活動の定着や製造現場の従業員のモラル向上へとつなげていきます。
5S活動の導入にあたっては、作業場の整理整頓や美化など「実行すること」自体が目的化してしまうケースがみられます。しかし、それでは単に職場がきれいな状態に保たれるだけで、大きな意味を成しません。
5S活動は本来、下記のような目的に向けて導入されるもので、現場にさまざまなメリットをもたらします。一方、「実行すること」だけに目が向くとかえって生産性を損なってしまうなど、デメリットにもなりかねないことも合わせて認識してください。
作業場に資材や工具が乱雑に置かれている状態では、作業に必要なものを探すのにいちいち時間がかかってしまうなど、効率よく進めていくことができません。一方、資材や工具がわかりやすく定位置に置かれていれば、作業手順に沿って進めやすくなります。
また、ものを探すという作業がなくなることは、従業員のストレスの緩和やモチベーションのアップにもつながります。結果、作業が効率化されることで生産性も向上するでしょう。
資材や工具が乱雑に置かれた作業場では、作業中に思わぬ事故が起きるリスクを招きます。また、清掃や点検などの適切なメンテナンスが行われていない状態で工具や製造機械を使うと、劣化や不具合が起きている可能性が高まるため危険です。
5Sには作業場を安全な環境に整えて、労働災害を防ぐという目的もあるのです。
たとえば、ゴミが落ちていても放置するのが当たり前のような状況では、作業環境はますます荒れていってしまい、大きな事故にもつながりやすくなります。そこで5S活動を実施して作業場の整理整頓やメンテナンスなどの活動に取り組むことで、従業員一人ひとりの作業環境の整備への意識を高めていきます。
また、5Sをルールとして守るという風土が生まれれば、主体的に作業環境が整うようになります。職場環境が整うことで、従業員のモチベーションも高まり、離職率の低下といった副次的な効果も期待できるでしょう。
5Sは製造業から始まったものとされており、QSDの向上や保全業務との連携のほか、最近ではIoT化の推進への寄与など、製造現場にさまざまな効果をもたらしています。
5Sの導入は、生産管理において重要な3つの要素であるQCDの向上に効果的です。なおQCDとは、以下の頭文字をとった言葉です。
5Sによって作業環境が整うことで、従業員が集中して作業に取り組めるようになり、品質の向上が見込めます。資材や工具を探す、あるいは見つからないことで追加発注してしまうといった無駄をなくすことで、コスト削減にもつながるでしょう。さらに、適切な場所に資材や工具が置かれていれば作業効率がアップするため、コスト削減だけではなく、納期の短縮にも効果的です。
5S活動の実施の際は保全業務との連携を図り、異常を早期発見し対処する体制構築に役立てましょう。
例えば5Sの「清掃」では、作業場や製造機械などを清掃するだけではなく、製造機械の点検を実施項目に盛り込みます。こまめに清掃を行うことで、いつも汚れない箇所に油汚れが付着している、床にボルトが落ちていたといった異常を示すサインにいち早く気づけるようになるでしょう。
この時点で、こうした異常を保全業務の担当者に伝えて修理などの対処が行われれば、製造機械の大きな不具合、あるいは大量の不良品の発生といった事態を防げます。
5Sによる現場改善に対するマインドの向上は、IoT化の推進にも役立ちます。
製造業におけるIoT化の主な目的は、製造機械の稼働管理といった見える化・自動化にあります。IoT化を進めるにあたっては、5Sの徹底により製造現場の無駄が省かれていることが前提となるでしょう。
5Sは、トヨタ自動車がトヨタ式生産方式の基本となるジャストインタイムの検討過程において、無駄をなくすためにスタートした施策といわれています。
トヨタ自動車による5Sでは、単に不要なものをなくして整然と必要なものが並べられているのではなく、誰が見ても何がどこにあるかすぐにわかり、簡単に取り出せる状態を目的としています。つまりトヨタ自動車では、ものを探す従業員がいないだけではなく、ものを取り出すために他のものを動かして運ぶという無駄まで省かれているのです。
さらに、汚れない状態を維持するため、汚れやゴミの原因への対策を図っていることも、トヨタ自動車の5Sの特徴です。
5Sはいまでは製造業のみならず、さまざまな領域で導入されています。一例として挙げられるのは看護の分野です。
看護においても、5Sの「整理」「整頓」「清掃」「清潔」「しつけ」の5つの項目は基本的には同じです。例えば、患者への薬品の誤投与は、薬が決まった場所に保管されていないことが原因で起こる可能性があります。また、看護師は交代制での勤務ですが、整理整頓がされていない状況では引継ぎのためのメモが他の書類に埋もれてしまって気づかないといったことが起こり得ます。
交代制やチーム制をとる看護の現場においても、5Sによるルールを守ることが、薬品や用具の取り違い、伝達ミスなどに起因する医療ミスの防止につながるのです。
従業員に浸透させて意義のあるものにしていくため、5S活動の導入にあたっては段階的なステップを踏んでいくことが大切です。まずは体制づくりからスタートして、目標設定やプロセスの改善を行ったうえで、チェックリストによる見える化を図っていきます。
5S活動を始めるにあたっては、まず、5S委員会を設置して職場リーダーを決めるなど、5Sを推進するための体制づくりを行います。そして、改善ボードを設置して、5S活動の目的や方針、体制などの周知や、進捗状況の共有のために活用します。
また、5Sでは「整理」において、保存するものと廃棄するものに分けますが、「何かあったときに役立つから」という考えで何でも保存してしまっては改善が進みません。「整理」における保存するものの基準策定など、5S活動の進め方についての理解を促進していくことも大切です。
次に、5S活動の目的や意義を従業員が共有できるように目標設定を行います。初めから高い目標を設定するのではなく、3段階に分けて設定していくアプローチが検討されるでしょう。
1段階目は、5S活動を始めた時点では整理整頓が行われていない状況の場合です。「整理整頓を徹底して清掃が行き届いた状態にする」といった目標を掲げます。
職場環境が整った2段階目では、「不良品率を低下させる」、「○○の作業の〇分の短縮」など、5S活動による具体的な成果が見える目標とします。
そして、3段階目では「リードタイムの短縮による生産性の向上」といった、5S活動による最終的な目標を設定します。
5S活動をスタートした後は、現状の方法に対して改善案の計画・実行・評価・改善を行い、新たなルールに変更していくことが必要です。たとえば、「整頓」で工具や部品を定位置化するため、道具や部品入れと置き場所に同じ色のシールを貼ったところ、わかりにくくて混乱を招いた場合には、置き場所にしまうものの写真を貼るといった改善案が考えられます。
なお、プロセスの改善は、「整理」「整頓」「清掃」「清潔」「しつけ」の順に行うと、スムーズに進めやすくなります。
PDCAサイクルを回してプロセスの改善を図り、5S活動の形が定まった段階でチェックシートによる見える化を図ります。チェックリストを作成し、どのレベルを求めるのか基準を明確化するのです。
チェックリストは「整理」「整頓」「清掃」「清潔」「しつけ」の大項目のそれぞれに対して、小項目を設けていく形です。製造業における一例は以下の通りです。
こうした項目ごとに、1点から5点の5段階といった形で数値化し評価を行います。部署ごとにチェックリストによる評価を行うことで競争意識を芽生えさせ、5S活動の浸透につなげていくとさらに効果的です。
製造業界では、5S活動を通じて作業環境を整えることで、作業の効率化による生産性の向上や安全性の向上を図れます。また、清掃とともに点検を行うことは保全業務との連携にもつながり、生産設備のチョコ停を防ぐ効果も期待できます。
なお弊社では、研修プログラムを通じて機械保全技能士2級レベルに相当する人材の育成およびアウトソースを行っています。より効果的な5Sの実施に向けて、保全に関する専門性を有する人材確保をお考えの企業様は、ぜひ弊社までご相談ください。
日研トータルソーシングでは、設備保全サービスにおける人材活用をトータルでサポートしています。充実した教育カリキュラムの導入によって、高い専門スキルを持った人材育成にも力を入れており、保全研修の外販実績も豊富にございます。
これら設備保全業務の人材不足問題を解決するための、弊社独自の取り組みをサービス資料としてまとめております。外部委託をご検討されている企業の皆様、ぜひ御覧ください。
お役立ち資料はこちら
年間研修実績10,000名を超える弊社が半導体・自動車業界の企業様から特に好評をいただいた「人材定着」に関する資料セットを作成しました。