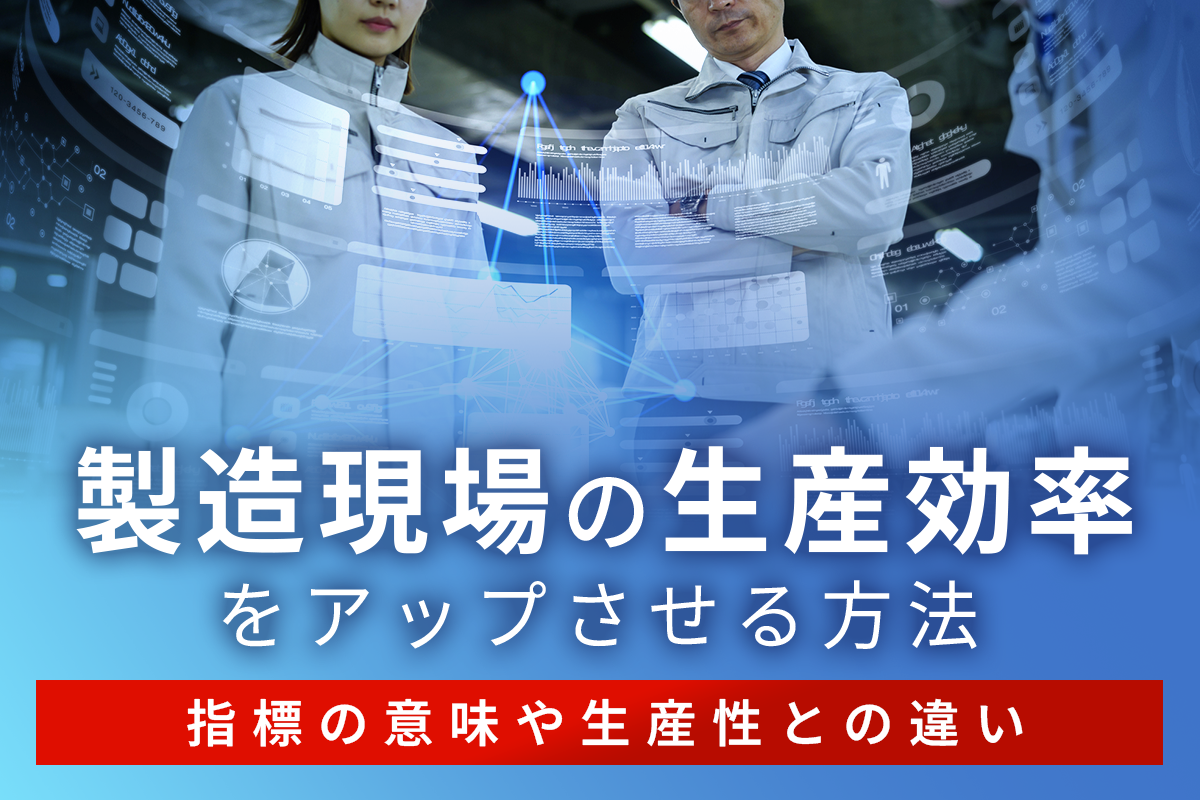
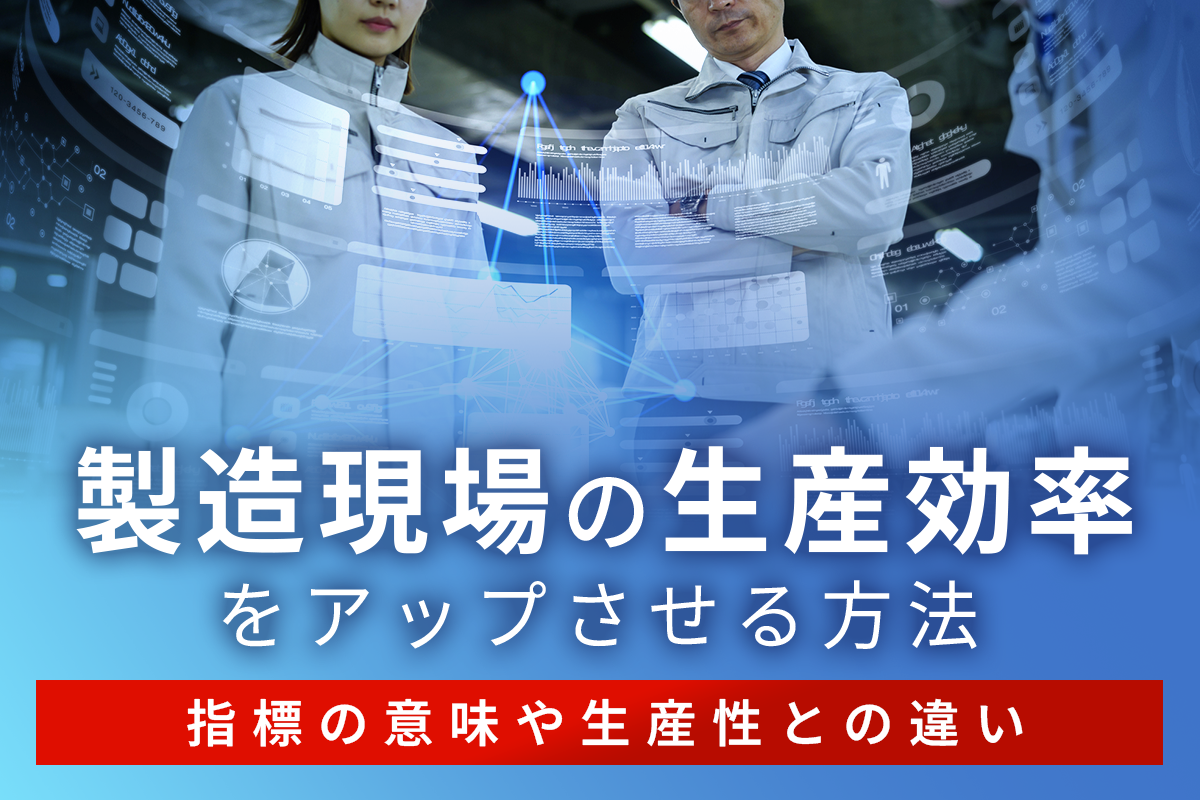
人手不足やIoT・AIといった技術の進歩など、大きな変革期を迎えている製造業では、業務改善に対して注目が集まっています。そんななか、耳にすることの多いキーワードが「カイゼン活動」です。
企業の生産性向上につながる取り組みとして知られる「カイゼン活動」は、ポイントを押さえて実践することが重要です。本記事では、「カイゼン活動」の意義や実践ポイントを具体的に解説します。導入方法に悩んでいる製造業関係の方は、ぜひ参考にしてください。
まず、カタカナで表記される「カイゼン」と漢字の「改善」にはどのような違いがあるのでしょうか。カイゼン活動への理解を深めるために、代表的な『トヨタ式カイゼン』を取り上げながら解説していきます。
カイゼン活動とは、生産性を向上させるために、作業の効率性や安全性などの見直しを行う活動を指します。
主に製造業の現場で取り入れられるカイゼン活動は、1951年にトヨタ式自動車が導入した「創意くふう提案制度」が発祥とされています。
「創意くふう提案制度」に始まった「トヨタ式カイゼン」では、加工や在庫におけるムダを排除し、従業員一人ひとりが主体的になって現場環境を構築していく仕組みをつくり上げました。
その後「トヨタ式カイゼン」は全国的に広まり、現在は製造現場のみならず、さまざまな業界で取り入れられています。2003年には、イトーヨーカ堂が豊田自動織機 の社員から指導を受け、売場運営に適用させた事例もあります。
また、カイゼン活動は日本国内にとどまらず、「KAIZEN」として世界的に広まり、多くの企業が注目しています。
トヨタ式カイゼンについて詳しく知りたい方は、こちらの記事も参考にしてください。
一般的に使われる「改善」は、課題点を洗い出し、その課題点を解消していくことを意味します。一方の「カイゼン活動」で目を向けるのは、課題点だけではありません。
“現状として大きな課題点がなかったとしても、より良い環境構築のために変化させていく取り組み”を、「カイゼン活動」というのです。
具体的には、「より良い作業工程にするためのポイントは何か?」「ケアレスミスを防ぐためには何ができるか?」など、従業員自らが課題や向上ポイントに気付き、カイゼンを繰り返していきます。
つまり、カイゼン活動とは終わりのないもので、常に意識すべき概念ということです。
実際にカイゼン活動を現場に取り入れる際には、どのようなポイントがあるのでしょうか。基本として、カイゼン活動は以下のPDCAサイクルに沿って行います。
前述の通り、「カイゼン活動」に終わりはありません。PDCAサイクルを回しやすい仕組みを整えていきましょう。
カイゼン活動には、以下2つの方式があります。
トップダウン式 | 企業の上層部や担当部署が指示を出してカイゼンしていく方式 |
ボトムアップ式 | 現場の従業員などが主体となりカイゼンを提案実施していく方式 |
カイゼン活動の目的には、従業員のモチベーション向上や実践的な課題点の把握も含まれています。そのため「トヨタ式カイゼン」でも採用されているボトムアップ式で実施するのが、理想的な形です。
ボトムアップ式のカイゼン活動を実践することにより、従業員は自ら仕事の進め方を考え、アイデアを出すようになります。結果として、「意見を伝えやすい環境」「現状把握に基づいた改善施策の実施」など、従業員にとってもより良い職場環境の構築につながるでしょう。
カイゼン活動を行うなかでは、社内で提案実施されたカイゼンの事例を共有することも重要です。
社内報などを利用して実際に従業員から挙がった改善案を紹介し、「どのような問題に、どのような対策を実行したのか?」を共有します。
事例の共有は、PDCAにおける「改善計画の立案&実行」「改善内容の評価と更なる課題の確認」にあたります。
異なる部署のカイゼン活動の実績を知ることで、新たな視点からのアイデアが生まれるかもしれません。
共有時には、実績を数値で示すこともおすすめします。たとえば、特定の業務にかかる時間を計測し、「カイゼン後には15分の時間短縮ができた」などと、カイゼン活動での変化を見える化していくと、カイゼン活動のメリットを実感しやすくなるでしょう。
従業員が自主的に取り組むことで、ボトムアップ式のカイゼン活動は成り立ちます。
そのため、従業員の意欲はカイゼン活動に欠かせない要素です。
カイゼン活動での成果を人事評価に反映させることは、従業員の意識を高める1つの方法となります。
「カイゼン」に取り組もうとするとき、まず何から着手するべきか悩む方も多いでしょう。
製造業でカイゼン活動を行う際、最初の取り組みとして多く選ばれるのが「5S」や「3M」です。この項目では「5S」と「3M」について詳しく解説していきます。
カイゼン活動を進める土台を作るために、「5Sの徹底」から始める企業が多いです。
整理 |
必要なものと不要なものを分け、不要なものを処分すること |
整頓 |
必要なものを決められた場所に配置して使うこと |
清掃 |
職場や道具を常にきれいに保つこと |
清潔 |
整理・整頓・清掃が正しく行われた状態を維持すること |
躾 |
職場のルールを明確にし、習慣化させていくこと |
カイゼン活動の基盤として5Sを徹底する際には、目的意識を持つことが重要です。
たとえば製造業の現場における「整理」には、在庫管理の目的が含まれます。また廃棄物の放置をなくすことによって、現場の安全性も高まるでしょう。整理・整頓・清掃が「躾」によって習慣化されていれば、作業効率を向上させられます。
これら5Sの裏に隠れた目的までを意識した行動を醸成するためには、従業員に「意識してください」と伝えるだけでは不十分です。
整理のために在庫数や作業の進捗状況を可視化する、システムを導入するなど、改善状況を見える化する仕組みを作ることが重要なのです。
カイゼン活動の基盤作りには、「3Mの削減」も重要です。
3Mとは、ムリ・ムダ・ムラを指し、それぞれ以下の意味を持ちます。
ムリ |
作業者および設備に対し、能力以上の成果を求めること |
ムダ |
効率を下げている不要な作業や過剰生産のこと |
ムラ |
作業者によって品質にばらつきが生まれること |
製造業における「ムリ」は、作業者に負担がかかりすぎている状況や、設備への過負荷などが挙げられます。これは生産性や品質の低下だけではなく、ヒューマンエラーによるミスの増加や事故の誘発など、多大なリスクが潜む要素です。
「ムダ」には、作業工程で発生する不要な運搬や在庫、製品に付加価値を与えない加工などが含まれます。
各プロセスにおける適切な人員配置や生産ラインの見直しによって3Mを削減していくことは、結果として「カイゼン活動」につながっていきます。
製造業において「カイゼン活動」への取り組みは、品質向上やコスト削減など、多くのメリットをもたらします。
しかし、最初のステップで洗い出した自社の問題点に対し、具体的な改善策が見いだせない製造業関係の方も多いことでしょう。
そんなときには「日研トータルソーシング」にご相談ください。設備保全や開発、設計など、各製造業における課題に合わせたご提案をいたします。
半導体・電池業界の研修実績年間10,000名を超える派遣会社が「今後の製造現場を左右する情報」をまとめた資料セットを作成しました。