7つのムダとは?トヨタ生産方式の基本思想やムダを排除する方法
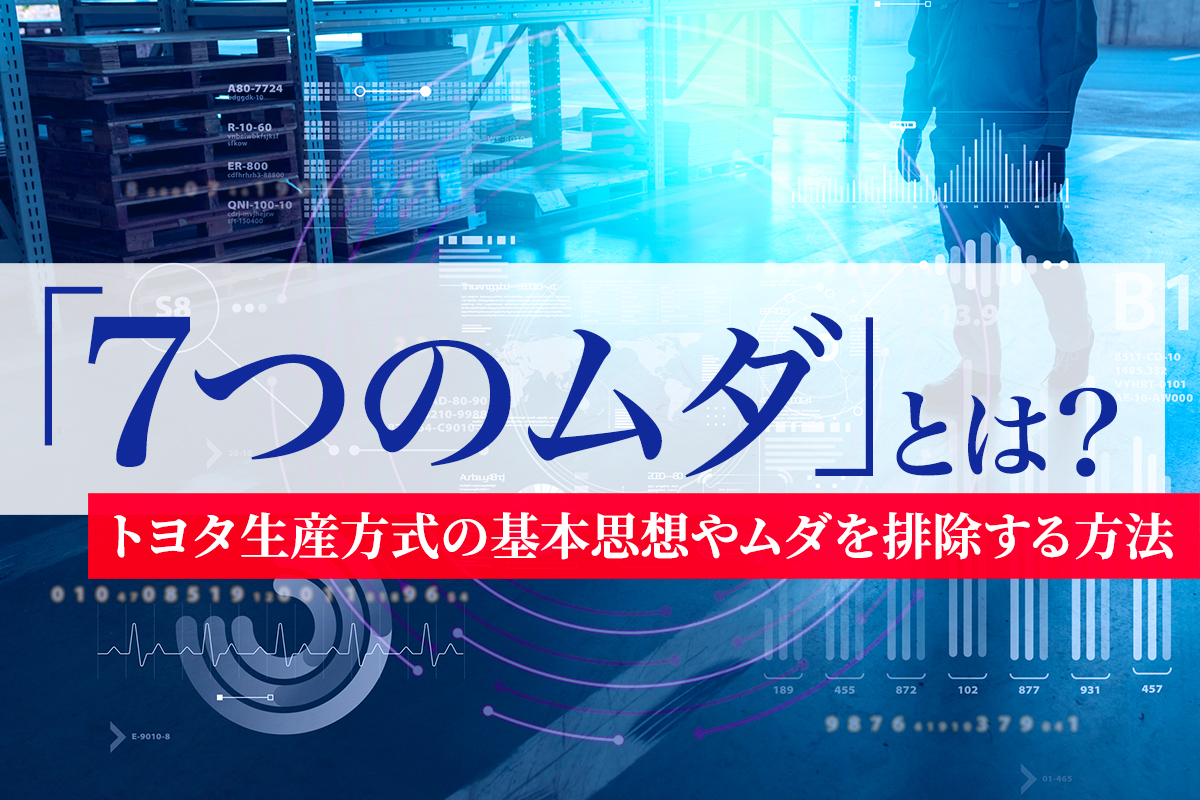
トヨタ生産方式とは、徹底的にムダをなくすことで生産性向上を目指す「モノづくりの考え方」です。
大量生産でコスト削減を図る一般的な生産方式との大きな違いは、顧客のニーズに合わせて「必要なものを、必要なときに、必要なだけ造る」点にあります。
トヨタ生産方式の主なメリットは「在庫の最小化」による「利益の最大化」です。管理費と人件費を抑えながら優れた業務効率を可能にするトヨタ生産方式は、いったいどのような構造で成り立っているのでしょうか。
本記事ではトヨタが長年改善を積み重ねて導き出した、現場改善のために取り除くべき「7つのムダ」について、トヨタ生産方式の基本思想から紐解いていきます。
トヨタ生産方式における「7つのムダ」とは
贅肉を削ぎ落し、引き締まった状態を表す英語「lean(リーン)」から「リーン生産方式」とも呼ばれるトヨタ生産方式。その理念を実現する手法の1つが「7つのムダ」です。
トヨタ生産方式を実現するために、7つのムダを含む、以下4つの手法を提唱し、実践しています。
7つのムダ | 生産の仕組みから「ムダ」すなわち「付加価値を生まない作業」を取り除くこと。 |
カイゼン | 不具合を解消するだけでなく、作業効率をより良くする仕組みを模索すること。 |
問題の見える化 | 問題が生じたときに、状況をただちに共有して職場全体で問題意識を持ち、解決に向かうこと。 |
なぜなぜ分析 | 課題に対して「なぜ」という質問を5回繰り返し、問題の根本を見極めること。 |
トヨタ生産方式の基本思想
トヨタ生産方式の柱となるのは「自働化」と「ジャスト・イン・タイム」と呼ばれる基本思想です。この2本の柱を製造プロセス全体に一貫させることでムダを省き、効率的な生産を可能にします。
トヨタ生産方式を取り入れるには、まずどのような理念に基づいているのか知ることが重要です。
自働化
自働化とは品質や設備にトラブルが起きたときに、機械が自らトラブルを検知して停止し、不良品の発生を未然に防ぐ仕組みです。
異常を発見して作業を中断させる仕組みは、単なる「動作」ではなく「働き」に相当することから、にんべんのついた「自働化」と名付けられました。
自働化を実現するためには人の手で製造工程を作り込むことが重要です。改善に改善を重ねて作業の簡便化を追求し「誰がやっても安全で確実な状態」に磨き上げてこそ、トラブルの少ない効率的な製造が叶います。
たとえばトヨタ生産方式の製造現場には、機械の稼働状況や作業指示がひと目でわかる電光掲示板「アンドン」が設置されています。
異常が発生するとアンドンに表示され、責任者は即時に状況を把握して対処に向かいます。製造途中の「仕掛品」の段階でトラブルを解消するので、不良品の発生が抑えられる仕組みです。
さらに、自働化した生産ラインでは人が機械に付きっきりになる必要がありません。ひとりが多くの機械を担当できるので、人件費の削減に効果的です。
JIT(ジャスト・イン・タイム)
ジャスト・イン・タイムとは「必要なものを、必要なときに、必要なだけ造る(運ぶ)」考え方です。
トヨタ生産方式の工場での部品補充は「使った分だけ前工程に取りにいく」ことを基本としています。各工程間で「どの部品がどれだけ必要か」を知らせる伝達ツールとして役立つのが「かんばん」方式です。
かんばんには「いつ・どこで・なにが・どれだけ」使われたのかが書いてあります。かんばんが取り付けられたケースから部品を使用した作業者は、そのかんばんを外して前工程に届けて部品の製造を依頼します。
かんばんの知らせにより作業者は必要最小限の部品を計画的に製造するため、「作りすぎのムダ」や「品質のばらつき」が予防されるのです。
かんばん方式はスーパーマーケットの商品補充からヒントを得たといわれています。すべては生産現場のムダ・ムリ・ムラを徹底的になくし、良いモノだけを早く効率よく造るため。まさに「トヨタ式のカイゼン」というべき仕組みです。
トヨタ生産方式におけるムダとは?7つのムダを排除する方法
生産効率化の成否は、いかにムダを最小限にできるかにかかっています。トヨタでは付加価値を生まない作業として「7つのムダ」を掲げており、それらの「ムダ取り」に力を注いできました。
次では7つのムダとその例、取り除き方について解説します。
加工のムダ
加工のムダとは、必要のない加工や検査のことです。作業者の時間と原材料にかかるコストが浪費されます。
・加工のムダの例
加工のムダには以下のようなものが挙げられます。
- あらかじめ接着剤が塗布されているネジに仕様が変更されたにもかかわらず、従来の手順のまま接着剤を用いてネジを固定している
- 原材料の鋼材に施された表面加工を剥がして組み付け、再び表面加工を施している
- 社内の検査体制が十分に整っているのに、慣例だからと外注で検査の依頼をしている
・加工のムダを排除する方法
加工のムダを排除する方法は以下の通りです。
- なぜこの加工が必要なのか
- より効率的な技術を採用できないか
加工のムダを排除するには、定期的な作業工程の洗い出しと見直しをします。慣習にとらわれずに改善の余地を探すことが大切です。
また、現状において最善の製造方法を定める「作業標準」の最新版を遵守しているかをチェックすることも、ムダの可視化と品質管理に有効です。
在庫のムダ
在庫のムダとは、製造業における主な在庫「原材料、部品、仕掛品、完成品」が余分に保管されていることで生じる、ムダな仕事を指します。余分な管理コストを生む原因です。
・在庫のムダの例
以下のようなケースが在庫のムダです。
- 原料の投入ミスが発生したときのために余分に原材料在庫を用意している
- 納期が短い顧客の発注に備えて完成品を保管している
・在庫のムダを排除する方法
在庫のムダを排除するのは、以下のような方法を実践します。
- 生産計画に基づいた在庫管理を徹底する
- 小ロットの発注に対しては、ひとつずつ後工程に回す『一個流し生産』を採用する
完成品の過剰在庫は仕様変更に対して柔軟な対応ができません。行き先のない在庫を抱えてしまうデメリットを避けるためにも、綿密な生産計画が求められます。
また「失敗したら予備を使えばいい」というという考えが定着してしまうと、失敗の多発が埋もれてしまい改善に結びつかない恐れがあります。ミスが起きにくい作業工程を練り上げたうえで、常に改善する意識を持つことが大切です。
関連記事:在庫管理が重要な理由とは?製造業の課題と効率化する際のポイント
不良や手直しのムダ
不良や手直しのムダとは、不良品の発生によって生じる手直しや処分、再出荷で生じるムダのことです。選別、回収、処分、再生産、原因究明、補償に至るまで、不良品の発生は莫大なコストを浪費するリスクがあります。
・不良や手直しのムダの例
不良や手直しのムダの例は下記の通りです。
- 製造機器の条件設定に誤りがあったため、製造分を廃棄した
- パーツの取り付けミスが1件発覚したため、対象期間の製造分を全件検査することになった
・不良や手直しのムダを排除する方法
不良や手直しのムダをなくすための方法は、以下のような方法を検討します。
- 作業標準を動画やOJTで説明し、作業者の理解度を深める
- 社内セミナーを実施して、作業クオリティの均一化を図る
- 品質管理のために生産ラインの要所に検査装置を取り付ける。(自働化の導入)
不良品の多くは人的ミスが原因で発生します。そのため、「いかにヒューマンエラーが起きない仕組みをつくるか」と「いかに不具合を早期に発見できるか」が重要です。
トヨタの事例では不良や手直しのムダを排除するために「自働化」を実装して、不具合の早期発見と解消に役立てています。
手待ちのムダ
手持ちのムダとは、作業者の手元に作業がない「手持ち無沙汰」な状態のことです。手待ち状態であっても人件費は発生します。また標準作業に手を動かしていたとしても、不必要な作業であれば、隠れた「手待ちのムダ」です。
・手待ちのムダの例
手持ちのムダの例には以下のようなケースがあります。
- 前工程の加工や原材料の入荷が遅延しているため、作業に取りかかれない
- 生産計画にばらつきがあり、作業量が極端に少ない日がある
- 機械のトラブルによる生産ラインの停止
・手待ちのムダを排除する方法
手持ちのムダを排除する方法は、以下のような方法です。
- 工程ごとの標準時間を正確に計測し、適切な生産計画を立てる
- 小ロット生産では仕掛品を溜めず、一個流し生産を適用する
- 製造機器の点検をルーティン化し、定期メンテナンスを実施する
手待ちのムダの原因は主に「作業の偏り」と「人員配置」です。工程間に作業量の差がありすぎると作業者同士のあいだに軋轢を生み、モチベーションの低下から生産効率を落としてしまう恐れがあります。
生産ラインがよどみなく流れるよう、データに基づいた綿密な生産計画を立案することが手待ちのムダを省くための第一歩です。
関連記事:工場における生産性向上のポイントは?求められる理由や改善の方法
造りすぎのムダ
造りすぎのムダとは、仕掛品や完成品を余計に製造してしまうことです。
造りすぎのムダは連鎖的に「在庫・動作・運搬のムダ」を生むため、7つのうちで最悪のムダと呼ばれています。造りすぎているあいだも作業は続くので「手持ちのムダ」が隠れてしまうことも問題です。
・造りすぎのムダの例
次のような場合は、造りすぎのムダが懸念されます。
- 機械の故障や、納期の短い発注に備えて予定より多く製造した
- 作業者が手待ちの状態だったので、注文は受けていないが製造しておいた
・造りすぎのムダを排除する方法
造りすぎのムダを排除する方法として有効なのが、以下のような方法です。
- 各工程の1日あたりの生産量と、完成品1つにかかる時間『タクトタイム』を算出し、データを基に適切な生産計画を立てる
- 完成品の保管場所を1ヵ所に定め、在庫状況を可視化する
- 棚卸しを定期的に実施する
「いつか使うから多めに」という考えを捨て、あくまで「必要なものを、必要なときに、必要な分だけ」造る姿勢の徹底が大切です。生産管理システムの活用も造りすぎのムダの回避に有効です。
動作のムダ
動作のムダは、しゃがむ、立つ、探す、持ち運ぶ、持ち変える、調べる、など、製造の進捗に関係しないすべてのムダな動作を指します。不要な動作は作業者にも負担を強いるので、生産性を保つためには積極的に省きたいムダです。
・動作のムダの例
動作のムダには、以下のような例があります。
- 連続する作業Aと作業Bの作業台が離れている
- ひとつの作業で何度も工具を持ち替える
- 手順に不安があるため、事務所に戻って作業標準を確認した
- 工具が見当たらないため、工場内を探す
・動作のムダを排除する方法
動作のムダを排除するには、以下のような方法を実践します。
- 作業スペースのレイアウトや作業標準を見直す
- 工場内に作業標準を掲示する
- 作業場の整理整頓を徹底し、工具の定位置を定める
作業が停滞せずスムーズに流れるように作業環境を整えることが求められます。それでも動きにムダを感じる場合には図面の見直しを検討しましょう。
運搬のムダ
運搬のムダとは、モノの余計な移動で生じるムダのことです。
モノを置く、積み上げる、持って移動するなど、運搬に時間がかかるほど「手待ちのムダ」発生のリスクも高まります。
・運搬のムダの例
運搬のムダの例は下記の通りです。
- 納品された資材が仮置き場を経由して保管されるため、運搬が二度手間になる
- 完成品の在庫数が多いため、製造するたびに別の倉庫へ運んで保管している
- 前工程と後工程の作業場の距離が離れており、仕掛品の運搬に時間がかかる
・運搬のムダを排除する方法
運搬のムダを排除するには、以下のような方法が有効です。
- 動線を考慮して各工程の作業場を配置し、製造品の総移動距離を短くする
- 造りすぎでモノが停滞しないように適正な在庫量をキープする
入荷から出荷まで、配置場所の選定でいかにスムーズな作業の流れを作られるかがポイントです。「在庫のムダ」や「造りすぎのムダ」を減らすことも「運搬のムダ」発生の低減につながります。
7つのムダの排除こそ、トヨタ生産方式の成否を分けるカギ
トヨタ生産方式の基本思想と手法のすべては7つムダの排除に結びつきます。なぜなら、トヨタが目指す「良い製品だけをタイムリーにお客様に届ける」という理想がムダの排除なしには実現しないからです。
7つのムダを排除することで全体の作業量をコンパクトに保ちます。モノの停滞をなくし、作業の流れを円滑にして効率的に生産可能です。
人材不足の深刻化とテクノロジーの進化が加速する現代社会にこそ「トヨタ生産方式」は必要とされています。