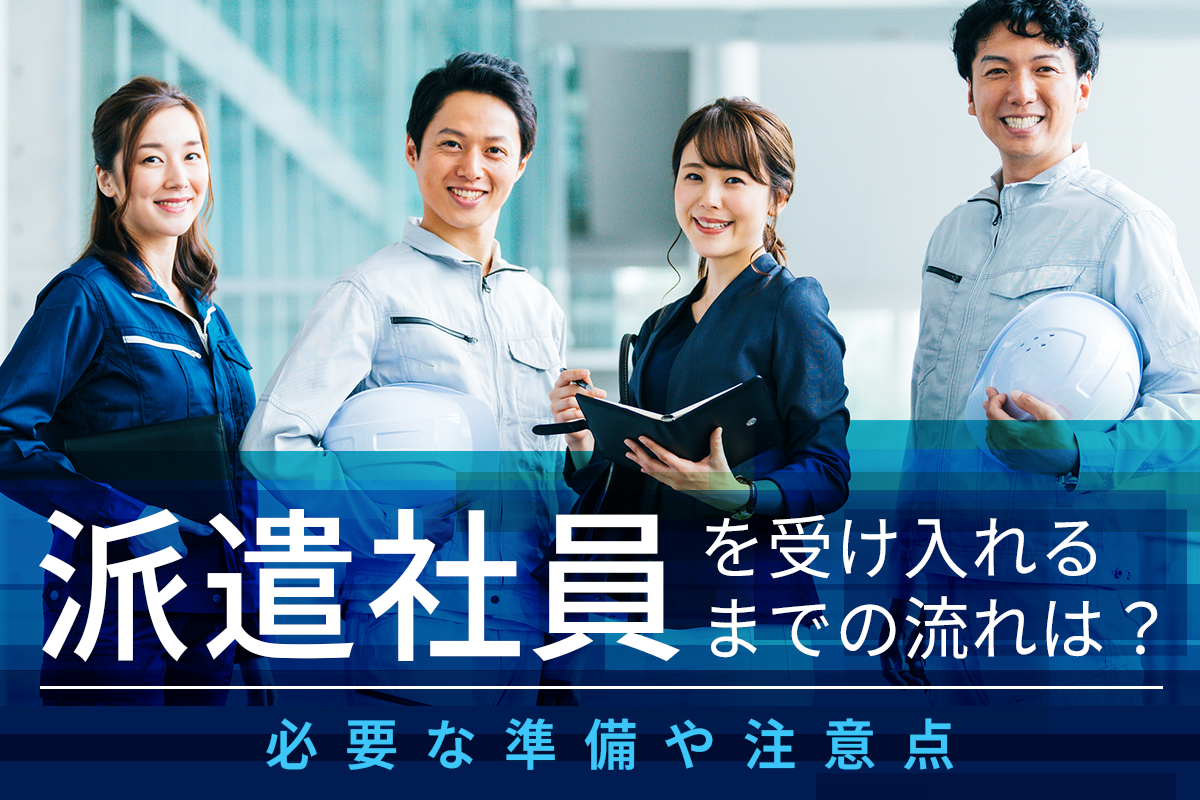
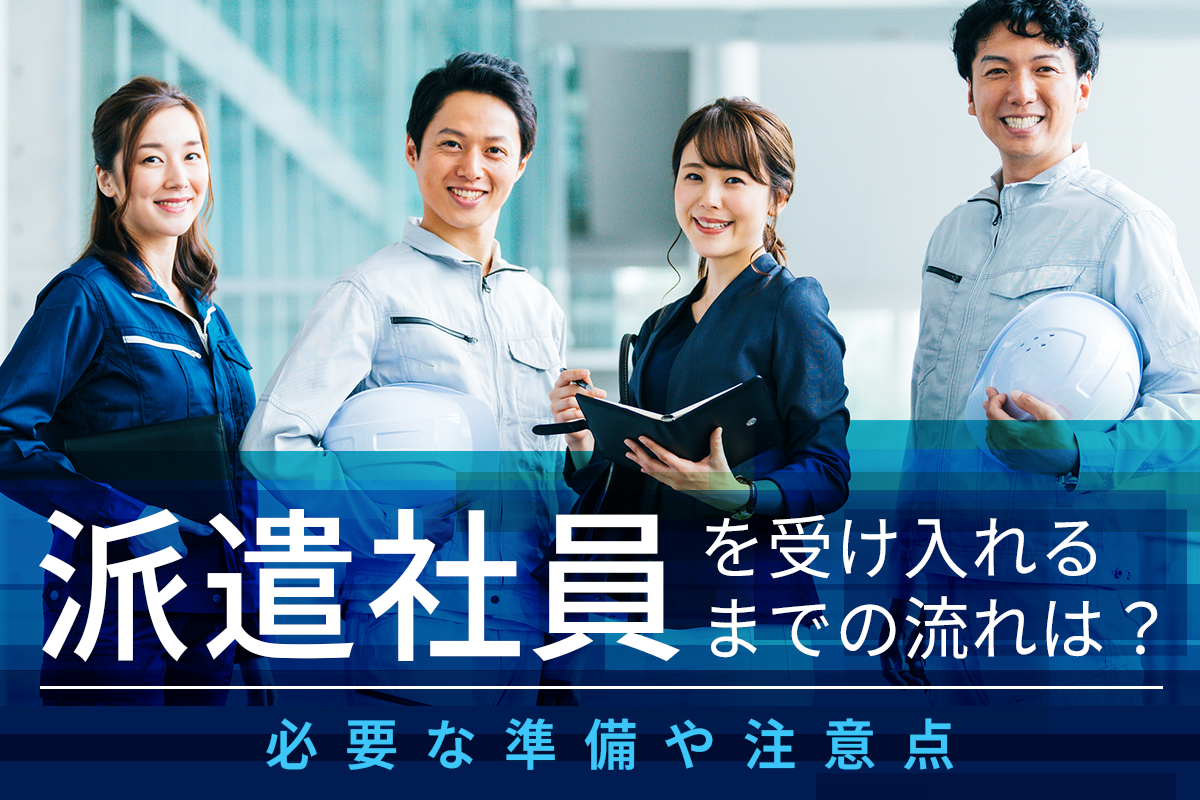
深刻化が増す人手不足に対処し、市場における競争力を強化すべく、製造業の現場では業務改善を通じた生産性の向上が常に求められます。製造業を中心に業務改善に用いられているフレームワークのひとつが「ECRS」です。
本記事では、ECRSを活用し業務改善を図るメリットや施策の進め方を考察し、業務改善の具体例などを見ていきます。
ECRS(読み方:イクルス)とは、業務改善の4原則を示すフレームワークです。以下の4つの言葉の頭文字から構成される戦略的な枠組みで、この順番にて課題を抽出し、業務改善を推進します。
ECRSの活用範囲は幅広く、近年では業種・業態を問わず多様なビジネス領域にて採用されていますが、元来は製造業が発祥です。課題抽出ならびに業務改善を図り、生産性向上を図るために用いられていたことが起源とされています。
業務フローの改善による業務効率化や、ミスの削減による品質向上など、ECRSの活用は製造業にさまざまなメリットを還元します。主に次の目的やメリットを背景に、多くの企業にてECRSが導入されています。
進めなければならない業務改善。しかし、滞積する課題にいざ直面すると、「何から始めたらよいのか」と、着手を前に戸惑ってしまうケースは少なくありません。
その道筋をつけるのがECRSです。ECRSは以下の視点の順番に準拠し、課題抽出ならびに改善施策に取り組むフレームワークであり、優先順位の整理やマイルストーンとして機能します。
基本的にこの順番に則り施策を展開していくことで、効率のよい業務改善が推進されます。
半ばルーティン化した日々の業務のなかには、前任者から引き継いだ結果、「なんとなく」やっている作業が含まれているケースは多いです。
また、同じ作業者が実施した方が効率的であるにも関わらず、担当者が分かれている作業や、一部の業務を別の作業者に割り振ったほうが合理的な業務フローもあるでしょう。
ECRSのフレームワークに従って業務を棚卸しし、一体化あるいは分離するほか、不要な業務を排除することで作業分担をより適切な方向へ見直せます。
作業や業務フローが煩雑化すると、担当者の固定化、業務の属人化を招きます。これは全体最適からは程遠い状況です。担当者が急に休んだときや退職したときに、作業が大幅に滞るリスクなども懸念されるでしょう。
ECRSを活用し不要な作業を省くなどして、業務フローの極力の単純化が望まれます。業務をマニュアル化し、業務分担を整理することで、作業の属人化を防止し全体最適を推進します。
ECRSのフレームワークに則り業務のムダを省き、シンプルな作業、単純化された業務フローへと改善を図ると、業務単位でもシームレスな連携が生まれます。業務全体の合理化が図られることで、作業ミスなども削減されるでしょう。
さらに、作業ミスの削減は品質向上やさらなる業務効率化などの副次効果をもたらし、好循環を生み出します。
ムダな業務の削減や業務分担の見直しに伴い、全体の業務量も軽減されます。それは人件費の圧縮や省力化、コスト削減にも還元されるものです。
結果、人手が不足している部門への配置転換なども可能となり、限られた経営資源の有効活用を推進します。
ESRSのフレームワークに則った業務改善は、頭文字の順番に沿って検討、実行へと移していくフローが基本です。
まず、「Eliminate(排除)」では、取り止めても問題のない不要な業務を検討します。続く「Combine(結合と分離)」では、一体化した方が効率的な類似業務や、、反対に分割した方がよい業務を特定します。
そして、「Rearrange(入替えと代替)」で検討するのは、業務の順序や場所、担当者などの入れ替えに・整理による業務効率化です。最後の「Simplify(簡素化)」では、パターン化や自動化による業務の単純化を実施します。
Eliminate(排除)では、各自が担当する業務の目的や実施している理由をあらためて整理し、不要な業務を洗い出し、取り止めても問題のない業務を検討します。たとえば、前任者から受け継がれてきた業務のなかには、すでに目的自体が不明瞭化している作業が含まれているかもしれません。
「排除」は業務負担の軽減やコスト削減に直結する、一番初めに着手するステップとなります。
Combine(結合と分離)では、複数の担当者が実施している類似業務を一体化することで、効率化が図れないか確認します。一方、担当者を分けて実施したほうが効率的な複雑な業務も洗い出し、分離を検討します。
「結合と分離」のステップは、作業者にとっても仕事がしやすくなるメリットが大きく、コストもほとんど発生しません。
Rearrange(入替えと代替)では、作業の順序や場所、あるいは担当者を入れ替えることで、業務効率化を図れないか検討します。
「入替えと代替」のステップでは、従業員によっては担当業務の変更等も生じるものの、こちらも実行のハードルはそれほど高くありません。
Simplify(簡素化)では、一部作業のパターン化や、生産設備・FA機器の導入などによってラインの自動化を図り、業務の単純化を検討します。業務の単純化は、属人化の防止や品質の安定化など、製造業において大きな意味を持つことはいうまでもありません。
ただし、新たな機器やシステムの導入を伴う場合には、多大なコストが発生することから、「簡素化」は最後のステップとなっています。
ECRSによる業務改善の具体例として、トヨタ自動車と無印良品の取り組みを紹介します。
ECRSは、世界に轟く「トヨタ生産方式」と親和性の高いフレームワークでもあります。
トヨタ生産方式では、以下の2つの概念のもとで、高品質な製品を消費者へ迅速に届ける体制が構築されています。
この2つの概念の根底にあるのは、ムリ・ムラ・ムダをなくす、「徹底したムダの排除」の思想です。
トヨタ自動車では、ECRSの「Eliminate(排除)」に該当する、7つのムダ(加工のムダ・在庫のムダ・造りすぎのムダ・手待ちのムダ・動作のムダ・運搬のムダ・不良・手直しのムダ)の排除を徹底しています。
株式会社良品計画が展開する無印良品では、ECRSのフレームワークの「Simplify(簡素化)」に該当するマニュアル化によって、顕著な業績改善を成し遂げています。
かつて無印良品では、店長が有するスキルや経験、ノウハウの違いによって、店舗運営においても差分が顕在化してしまう課題を抱えていました。そこで実施されたのが、徹底的なマニュアル化による属人化の排除であり、業務のレベルアップと標準化を実現しました。
店舗の業務マニュアルの「MUJIGRAM(ムジグラム)」は2,000ページ、本社の業務マニュアルの「業務基準書」は6,600ページにも及びます。また、現場の改善点をもとに「MUJIGRAM」は更新され、スタッフの業務改善に対する意識の醸成にも役立っています。
ECRSは、頭文字の順番通りに施策を展開していくことで、課題抽出ならびに業務改善をシームレスに実現へと導く、具体的かつ機能的なフレームワークです。
なかでも「Eliminate(排除)」と「Combine(結合と分離)」は、大きな手間やコストをかけることなく着手できます。持続的な業務改善、生産性向上の取り組みの一環として、まずは業務の棚卸しから実施してみましょう。
半導体・電池業界の研修実績年間10,000名を超える派遣会社が「今後の製造現場を左右する情報」をまとめた資料セットを作成しました。